High Precision Engineering Ceramics
Engineering ceramic components have physical and mechanical properties, as well as thermal and chemical functions. They have precisely controlled chemical composition, are easy to process according to controlled fabrication techniques, and are easy to design in structure.
We are able to supply a wide variety of alumina, zirconia, silicon nitride and MACOR ceramic parts. Parts with different structures can be processed by molding processes such as dry pressing, hot pressing, isostatic pressing, tape casting, extrusion and ceramic injection molding, and then undergo secondary precision processing, such as fine grinding, CNC processing, laser cutting or metallization, to obtain ceramic parts requested by customers.
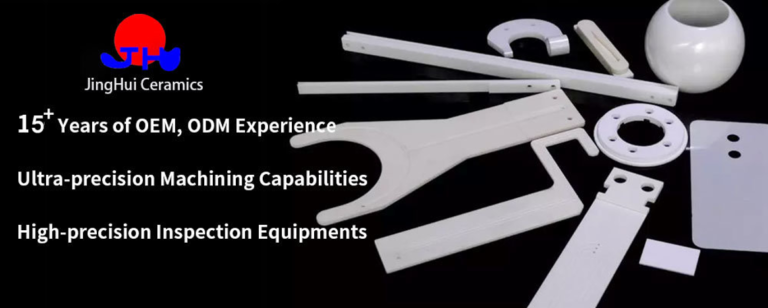
Table of Contents for this Page
It is not easy to introduce all aspects of engineering ceramics, so we have prepared a lot of information on this page for you to delve into. To make sure you can find the information you want quickly, we have prepared this content directory that will jump to the corresponding location when you click on it.
the Typical Applications
Engineering ceramic products have many advantages such as high temperature resistance, corrosion resistance, high pressure resistance, insulation, high hardness, wear resistance, low thermal conductivity, low specific gravity, etc., and are widely used in machinery manufacturing, power electronics, chemical industry, aerospace and other fields.
Hot Products Display
We classify Engineering Ceramics into 4 types:
1) Alumina Ceramic Parts
2) Zirconia Ceramic Parts
3) Silicon Nitride Ceramic Parts
4) Others
You can find the products you need from our classification.
Reference Cost Analysis
Wondering how custom engineering ceramic products are priced? Come and follow us to find out. In addition to the most important one – purchase price, you also need to consider transportation cost, tariffs and taxes and quality cost.
Purchase Price
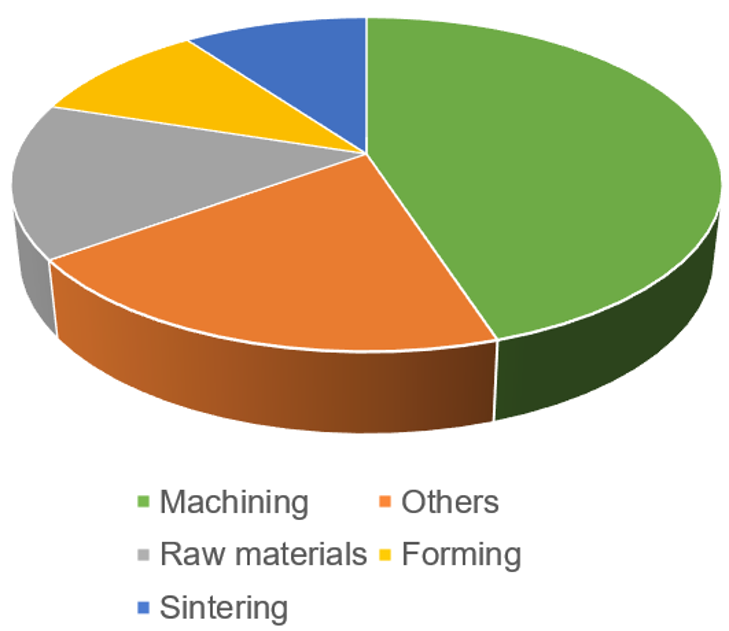
Remark:
– Others include fuel and power, equipment, labor, site fees, etc.
– The machining process has a direct impact on the production cost and accounts for the highest proportion.
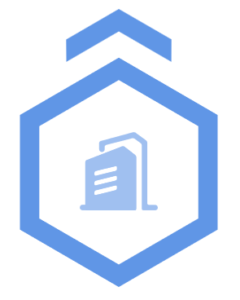
Transportation Cost
When choosing express, air, truck, train or sea, both cost and efficiency should be considered
Tariffs and Taxes
This cost is relatively fixed. Import customs code, national policies and agreements, the value of imported goods and types of imported goods will all affect the cost.
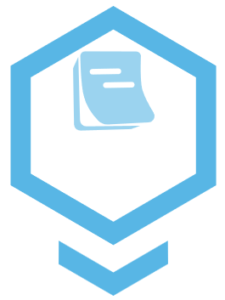
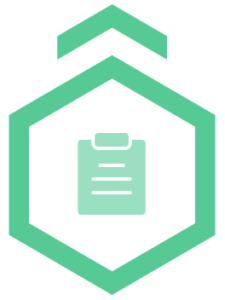
Quality Cost
This is a hidden cost and is easily overlooked. It arises if quality problems such as returns, replacements, and repairs occur.
Estimated Lead Time
1. Product customization process
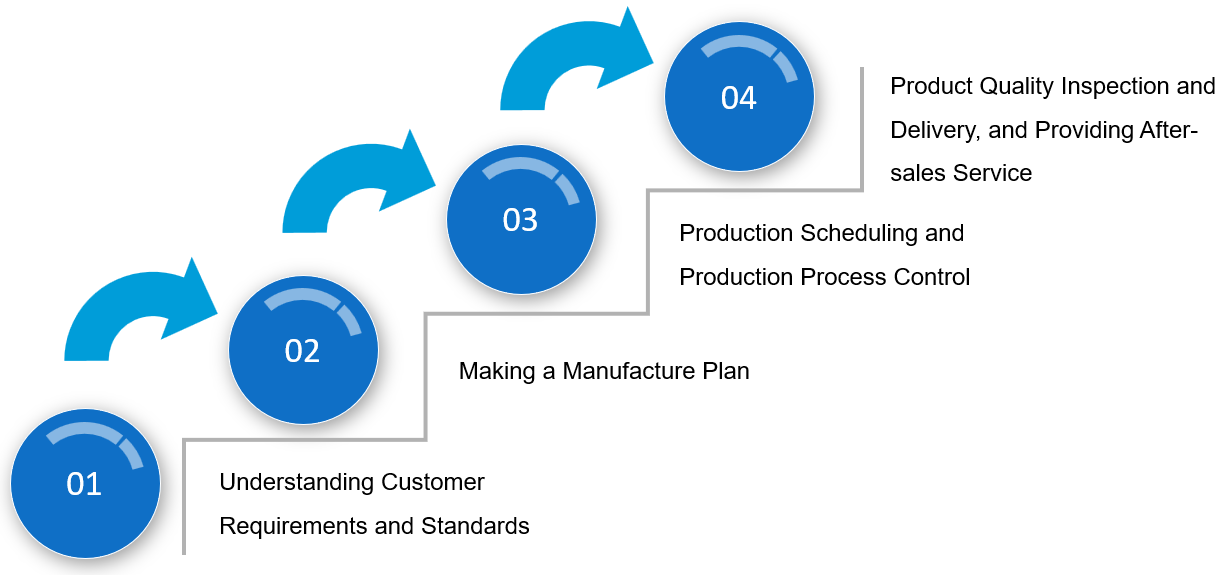
2. How long does it take from placing an order to receiving the goods?
Generally speaking, the production cycle of our customized products is usually 4-6 weeks, and the specific time depends on the actual situation, which will vary depending on factors such as product type, product structure, customized quantity and production process.
In addition, transportation time also needs to be considered. If expedited production or delivery is required, associated charges will be added. Therefore, it is recommended to consult the salesperson for a more accurate delivery time before placing an order.
Want to know how to compress lead times?
If you are not satisfied with the delivery time or need us to expedite the shipment, please contact our sales in time to communicate.
the Basic Knowledge
1. Common engineering ceramic materials and their applications
Engineering ceramics, also called structural ceramics, refer to ceramics that can be used as engineering structures and mechanical parts, which are different from ceramics in the traditional sense. Engineering ceramics are made of refined high-purity, ultra-fine, artificially synthesized inorganic compounds as raw materials, and are fired by a precisely controlled preparation process to have specific properties.
Common engineering ceramic materials include alumina, zirconia, silicon nitride and new engineering materials – machinable glass ceramics.
1.1 Al2O3 alumina ceramics
Alumina ceramics are the most widely studied and applied engineering ceramics, with high melting point (above 2000°C), high hardness (Rockwell hardness is HRA80-90, second only to diamond), good insulation performance (volume resistivity as high as 1014Ω·cm), good chemical stability and so on.
It is widely used as high-temperature structural materials, wear-resistant materials, electrical insulation materials and chemical corrosion-resistant materials, such as high-temperature kiln furniture materials, wear-resistant linings and grinding bodies, electric vacuum tube shells and ceramic substrates, etc.
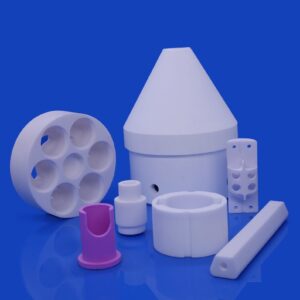
1.2 ZrO2 zirconia ceramics
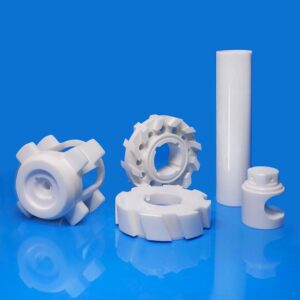
The thermal conductivity of zirconia is the lowest among common ceramic materials, and its thermal expansion coefficient is closer to that of metal materials, making it an important structural ceramic material. Its special crystal structure makes it an important electronic material.
Zirconia ceramics can obtain high strength and toughness through phase transformation and toughening. Partially Stabilized Zirconia (PSZ) ceramics are currently the ceramic materials with the highest strength and toughness, known as “ceramic steel”. Although the Fully Stable Cubic Zirconia (FSZ) ceramics are not as strong and tough as PSZ ceramics, they have been widely used as oxygen sensors, high-temperature heating elements, and high-temperature fuel cell diaphragms due to their good ionic conductivity.
1.3 Si3N4 silicon nitride ceramics
Silicon nitride ceramics is a kind of engineering ceramics that develops rapidly among non-oxide ceramics. Silicon and nitrogen are covalently bonded to form a tetrahedral structural unit, which makes the ceramics have high strength, high hardness, and excellent oxidation resistance and corrosion resistance performance.
Silicon nitride ceramics have good red hardness and are especially suitable for high-speed cutting or grinding on high-speed CNC machine tools. Compared with silicon carbide ceramics, silicon nitride ceramics have higher strength and toughness, and are more suitable for the preparation of ceramic products requiring high strength and high toughness, such as grinding media ceramic tools and bearings.

1.4 Machinable glass ceramics
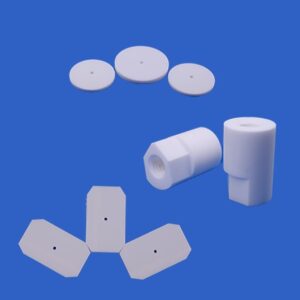
MACOR is a kind of glass-ceramic composite material with good density. It has processing advantages unmatched by other ceramics, and its machinability is very high, so it is named “machinable ceramics”. This kind of ceramic can be directly processed by conventional CNC milling cutter, and the material does not need to be heat treated after processing.
At present, this kind of ceramics is mainly used in electrical components, insulators, heating devices, welding fixtures, vacuum components and other parts, and the application fields cover aerospace, automotive, medical, communication and other fields. Although the performance of this ceramic is superior, it has not been widely promoted due to the high price of its material.
2. Preparation process of engineering ceramics
The preparation of ceramics is a process in which ceramic powder raw materials undergo a series of processing and finally become finished products. The production steps of engineering ceramics can be roughly divided into four steps: the first step is the preparation of ceramic powder, the second step is molding, the third step is sintering, and the fourth step is finishing.
2.1 Molding process of engineering ceramics
Ceramic molding is an important part of the engineering ceramics preparation process. The molding technology largely determines the uniformity of the green body and the ability to prepare parts with complex shapes, and directly affects the reliability of materials and the cost of final ceramic parts.
2.1.1 Factors to consider when choosing a molding method
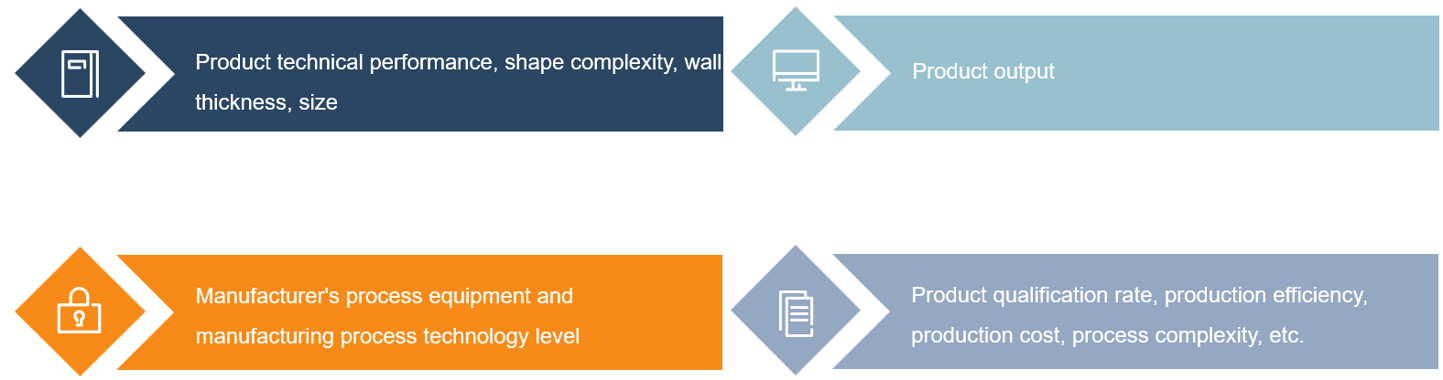
2.1.2 Common molding techniques
2.1.2.1 Dry pressing
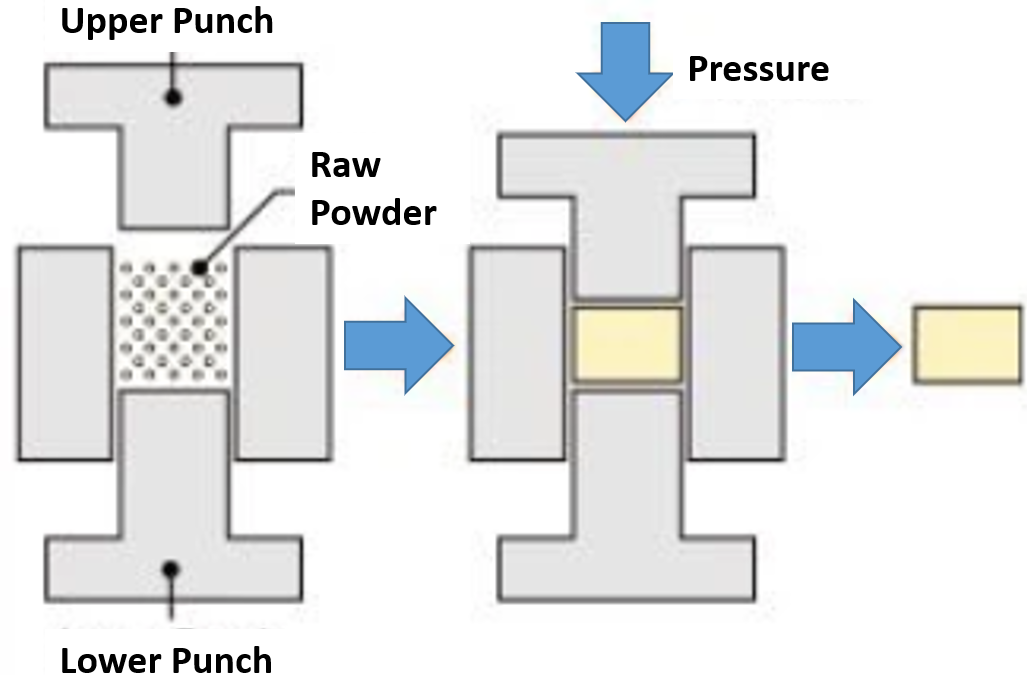
Dry pressing is to add a certain amount of organic additives (binders, lubricants, plasticizers, defoamers, water reducers, etc.) to the ceramic powder, and shape it in the mold under the action of external pressure.
Advantages | It is easy to realize automation, so it is widely used in industrial production. It is especially suitable for the preparation of various ceramic products with small cross-sectional thickness. |
Disadvantages | During the forming process, the uneven distribution of radial and axial pressure often causes the delamination, cracking, and uneven density of the green body. |
Application Examples | Ceramic sealing rings, ceramic valve parts, ceramic liners, ceramic linings |
2.1.2.2 Hot pressing
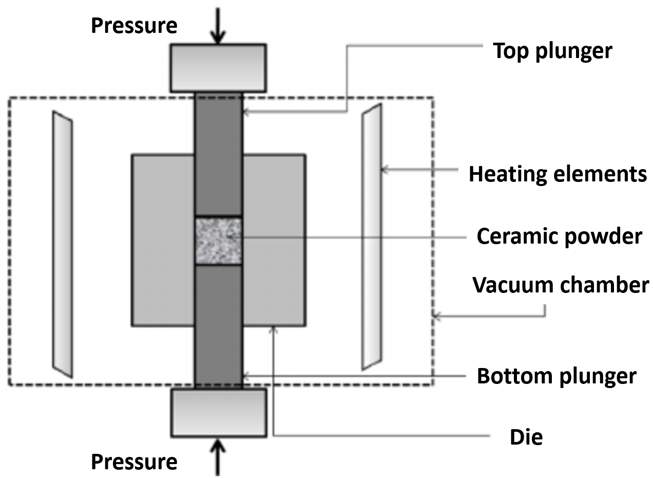
Hot press molding is to use the characteristics of paraffin wax to melt when heated and to solidify when cooled, to uniformly mix non-plastic barren ceramic powder with hot paraffin liquid to form a flowable slurry, inject it into a metal mold under a certain pressure, and cool it. After the wax slurry is solidified, the mold is demoulded, and the formed body is taken out. The green body is properly trimmed, embedded in an adsorbent and heated for dewaxing treatment, and finally sintered into the final product.
Advantages | Ceramic products with complex shapes can be formed, with high dimensional accuracy and almost no need for subsequent processing. It is the main molding process for making special-shaped ceramic products. |
Disadvantages | It is not suitable for the preparation of large-scale ceramic products, and it is difficult to prepare thick-walled products. High porosity and relatively many internal defects. |
Application Examples | Engineering ceramic parts of various complex shapes |
2.1.2.3 Isostatic pressing
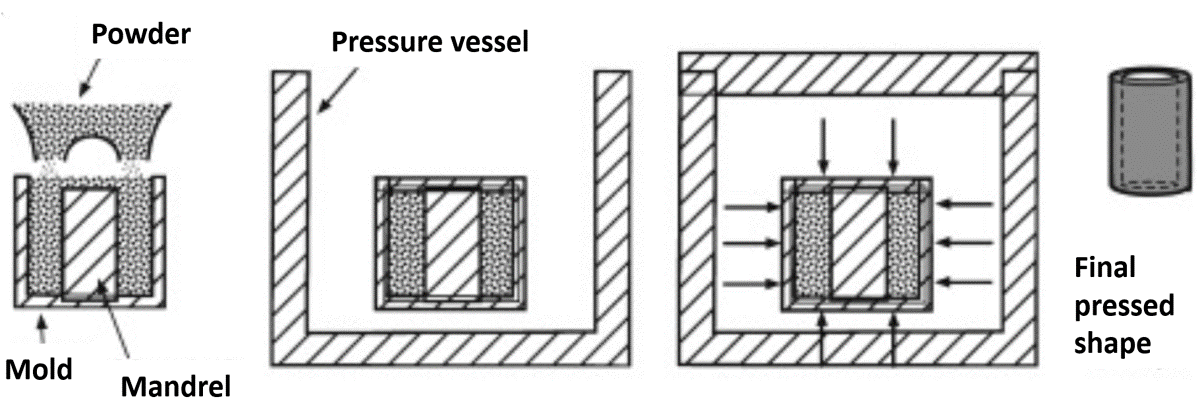
Isostatic pressing is a method of forming powder while compressing by applying isotropic pressure. According to different molding temperatures, isostatic pressing is divided into hot isostatic pressing and cold isostatic pressing. Cold isostatic pressing is an isostatic pressing method for forming workpieces at room temperature. Hot isostatic pressing refers to the isostatic pressing method of isostatically forming and sintering workpieces under high temperature and high pressure. The so-called isostatic pressing usually refers to cold isostatic pressing.
Advantages | It can press parts with concave, hollow, slender parts and other complex shapes; the density of the compact is evenly distributed, and the strength of the compact is high; the mold is easy to make, has a long life and low cost. |
Disadvantages | The size and shape of the green compact are not easy to control accurately, the productivity is low, and the investment is large, the operation is more complicated. |
Application Examples | Ceramic rods, ceramic sleeves, spark plugs, high purity alumina insulators |
2.1.2.4 Tape casting

Tape casting is also known as scraper molding. It is obtained by adding solvent, dispersant, binder, plasticizer and other components to ceramic powder to obtain a uniformly dispersed and stable slurry, and made a film of required thickness on a tape casting machine.
Advantages | The equipment is simple, continuous operation, high production efficiency, high level of automation, stable process, uniform properties of the blank film and easy control, suitable for manufacturing various ultra-thin ceramic devices, ceramic substrates, etc. |
Disadvantages | The green body has low density and high shrinkage. |
Application Examples | Alumina substrates for thick film and thin film circuits, structural ceramic thin sheets |
2.1.2.5 Extrusion molding
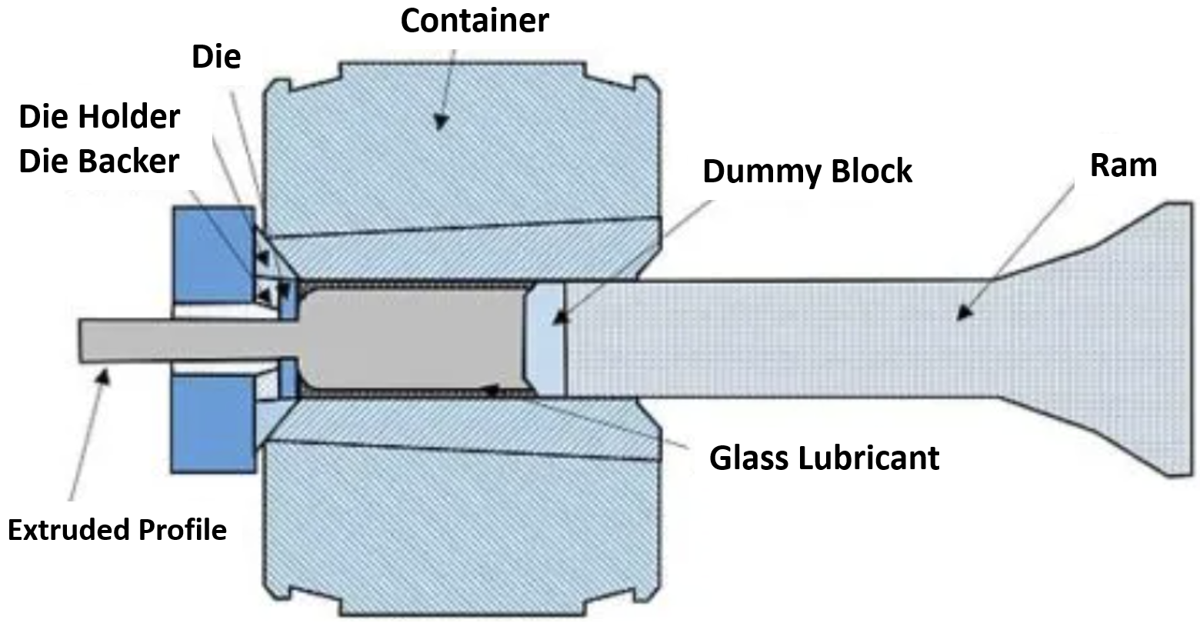
Extrusion molding is to mix powder, adhesive, lubricant, etc. with water evenly and fully, and then use a hydraulic press to push the piston, and extrude the plasticized billet from the extrusion nozzle. As the inner profile of the extrusion nozzle gradually shrinks, the piston exerts a large extrusion force on the mud mass, making the billet dense and formed.
Advantages | The product has a large porosity, density and compressive strength, and the pore size distribution is concentrated, and the gas permeation flux is very large. It is suitable for the manufacture of round, oval, polygonal and other shaped pipes or rods. |
Disadvantages | The material has low strength and is easy to deform, and may produce defects such as surface pits, blisters, cracks and internal cracks. |
Application Examples | Ceramic tubes, ceramic rods |
2.1.2.6 Ceramic injection molding (CIM)
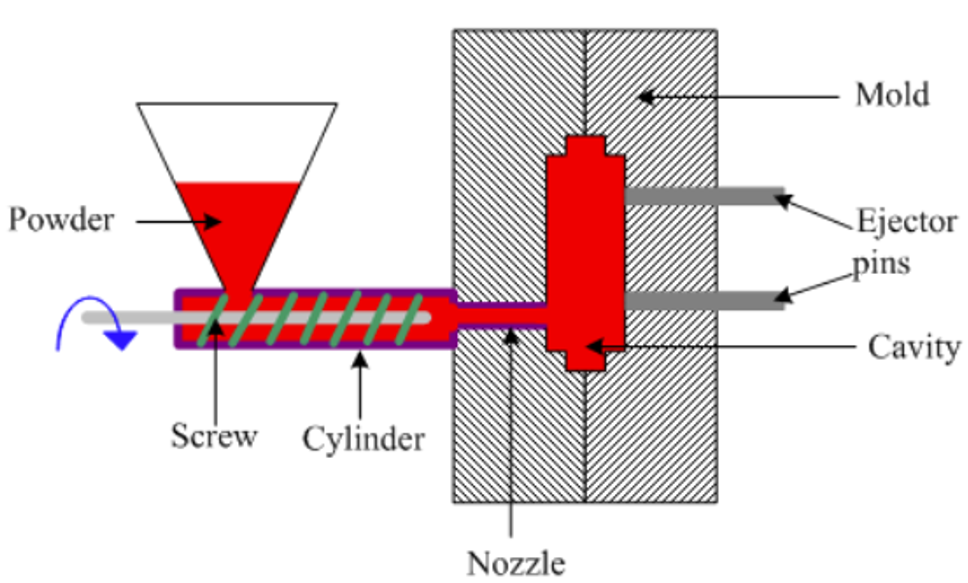
Ceramic injection molding technology is derived from the injection molding of polymer materials. It is molded by virtue of the characteristics of polymers melting at high temperatures and solidifying at low temperatures. After molding, the polymers are removed.
Advantages | It can manufacture high-precision ceramic parts of various complex shapes, and is easy to scale and automate production. |
Disadvantages | Because it contains a large amount of polymer binder, it is difficult to degrease the ceramic body, and there are disadvantages such as easy deformation of the blank and easy formation of pores. |
Application Examples | Various precision ceramic parts |
2.1.2.7 3D printing molding
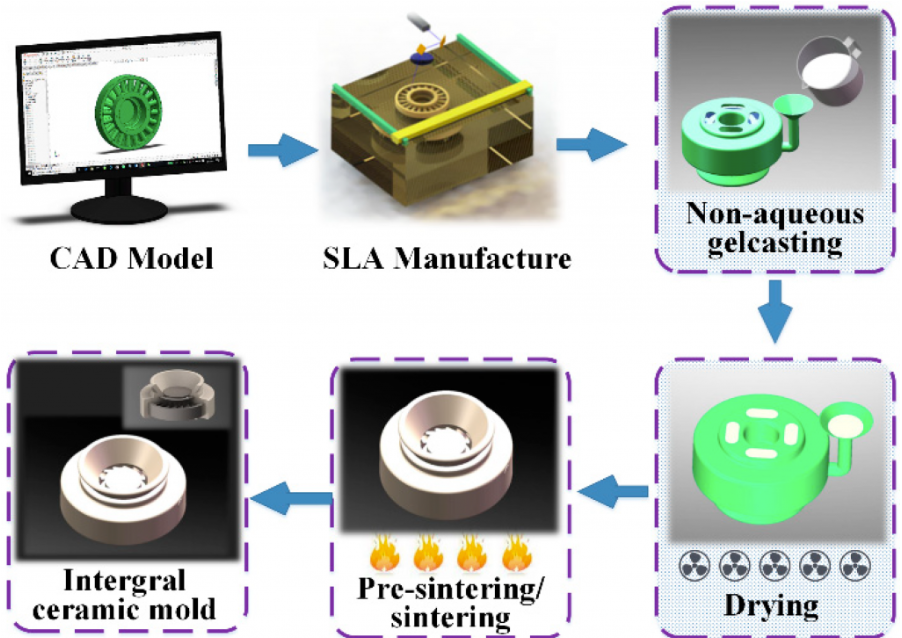
Ceramic 3D printing technology is also called Additive Manufacturing technology. It first discretizes the three-dimensional model data into multiple two-dimensional cross-sections, and controls the material through computer automation to manufacture parts in the way of point-line-surface-body gradual accumulation. This innovative manufacturing method allows the flexibility to create highly complex structures that cannot be achieved by traditional methods such as casting and machining.
Ceramic 3D printing technologies based on the principle of photopolymerization (ie SL, DLP and TPP) have shown great advantages in printing accuracy, part surface quality and mechanical properties. Therefore, it is considered to be the most promising type of ceramic 3D printing process.
Advantages | The manufacturing efficiency is high, rapid manufacturing can be realized, and the production cycle can be shortened. The waste of raw materials can be reduced and the cost can be reduced. |
Disadvantages | Ceramic 3D printing equipment and technology are still in the development stage, and there are certain uncertainties and risks. Equipment costs are higher. |
Application Examples | Ceramic Sensors, ceramic capacitors |
2.1.3 Comparison of various molding technologies
Various molding methods have different molding principles and processes, so their characteristics are also different, but each has its own advantages and disadvantages. The selection of engineering ceramics molding method should be comprehensively determined according to the performance requirements, shape, size, output and economic benefits of the product.
Molding Method | Molding Material | Product Shape | Product Size | Uniformity | Efficiency | Cost |
---|---|---|---|---|---|---|
Dry Pressing | Granulated powder | Flat | Small section thickness | Deviation | High | Lower |
Hot Pressing | Viscoplastic material | Complex | Small | Better | High | Low |
Cold Isostatic Pressing (CIP) | Granulated powder | Cylindrical, spherical | Big | Good | Medium | Medium |
Tape Casting | Slurry | Substrate | Thickness ≤ 2 mm | Good | High | Medium |
Extrusion Molding | Plastic material | Cylindrical | Long | Medium | High | Lower |
Ceramic Injection Molding (CIM) | Viscoplastic material | Complex | Small | Good | High | Medium |
SL Ceramic 3D printing Molding | Photopolymerization solution | Highly complex | Unlimited | Good | High | High |
2.2 Finishing technology of engineering ceramics
In order to achieve the precision of the product, most engineering ceramic products need further finishing treatment after the sintering process is completed.
2.2.1 Where are the difficulties in processing engineering ceramics?
Due to the extremely high hardness and brittleness of ceramics, it is extremely difficult to process. On the one hand, processing equipment and tools are easy to wear, on the other hand, it may also cause defects such as edge chipping and cracks during processing. For the difficulties in the processing of engineering ceramic materials, the following methods can be used to make breakthroughs.
2.2.2 Common finishing processes
2.2.2.1 Machining
2.2.2.1.1 Grinding
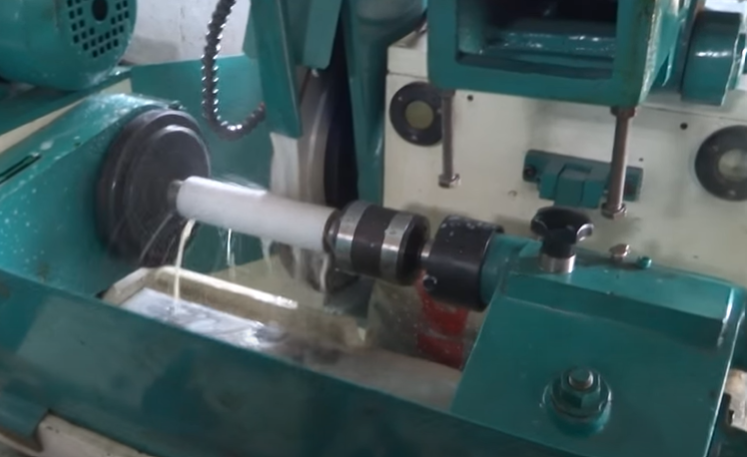
Grinding of ceramic materials is one of the most widely used processing methods at present. Grinding is a processing method that uses the cutting action of abrasive tools to remove the excess layer on the surface of ceramic materials and make the surface quality of ceramic materials meet the predetermined requirements. Common grinding forms usually include: external cylindrical grinding, internal cylindrical grinding, centerless grinding, thread grinding, surface grinding, forming surface grinding, etc.
2.2.2.1.2 Lapping
Lapping is a precision processing method between brittle failure and elastic removal. The lapping tool and ceramic material exert a certain pressure on the abrasive grains, and the abrasive grains roll and slide to remove a very thin margin from the ground ceramic material. It can grind flat surfaces, inner and outer cylindrical and conical surfaces, convex and concave spherical surfaces, threads, tooth surfaces and other profiles.
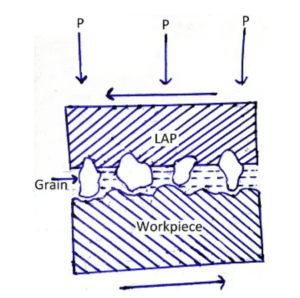
2.2.2.1.3 Polishing

Polishing is a processing method that uses polishing tools and abrasive particles or other polishing media to modify the surface of ceramic materials to reduce the surface roughness of ceramic materials to obtain a bright and flat surface. It is carried out within the elastic removal range of materials. Polishing cannot improve the dimensional accuracy or geometric shape accuracy of ceramic materials, but aims to obtain a smooth surface or mirror luster.
2.2.2.1.4 Laser processing
Laser processing uses a uniform laser beam with high energy density as a heat source to generate instantaneous high temperature at a local point on the surface of the processed ceramic material, and the local point melts or vaporizes to remove the material. Laser processing is a contactless, frictionless processing technology. No mold is needed during the processing, and the processing of three-dimensional complex shape materials can be realized by controlling the focus position of the laser beam on the surface of the ceramic material.
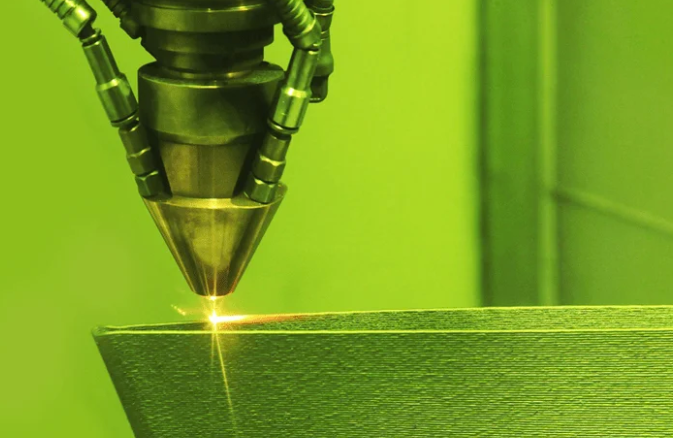
2.2.2.2 Surface glazing
The glaze coating can improve the insulation strength and mechanical strength, and is anti-fouling, moisture-proof and dust-proof.
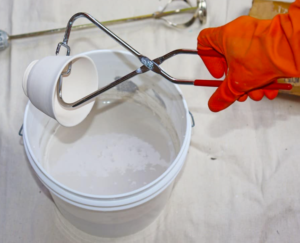
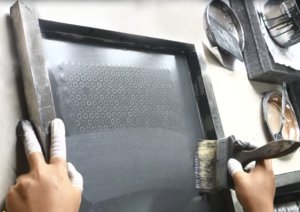
2.2.2.3 Metallization
Ceramic metallization is to firmly attach a layer of metal film on the surface of ceramics to realize the welding of ceramics and metals. A more advanced application is to print circuits on the surface of ceramics, which can transmit electric current.
3. Performance characteristics of engineering ceramics
3.1 Comparison of ceramic, metal and polymer structural materials
Ceramic materials, metal materials and polymer materials are three different structural materials, each with its own advantages and disadvantages, and suitable for different fields and needs. Here’s a comparison of them.
Comparison Point | Ceramic Materials | Metal Materials | Polymer Structural Materials |
---|---|---|---|
Material Properties | High hardness, wear resistance, corrosion resistance, high temperature resistance, good insulation, but high brittleness, prone to cracks. | Good toughness, easy to process and shape, good electrical and thermal conductivity, but easy to rust and corrode. | Lightweight, flexible, easy to process, poor electrical and thermal conductivity, but susceptible to heat and UV rays. |
Application Range | Rices, wheats, linseeds, sesame It is often used to make parts with high temperature, high pressure and corrosion resistance. Examples: mechanical seals, automotive engine parts. | The largest amount and the most widely used. Examples: steel (mechanical parts), aluminum alloy (aircraft, automobile parts, etc.), copper alloy (electrical equipment, auto parts), titanium alloy (high-end parts such as aerospace, medical equipment, etc.). | Commonly used in the production of plastics, synthetic rubber, synthetic fibers and other materials. Examples: Electronic equipment, automotive interiors, home appliances and other components. |
Cost of production | High | Medium | Low |
3.2 Performance parameters of engineering ceramics
The following is the performance parameters table of common engineering ceramic materials, for your reference.
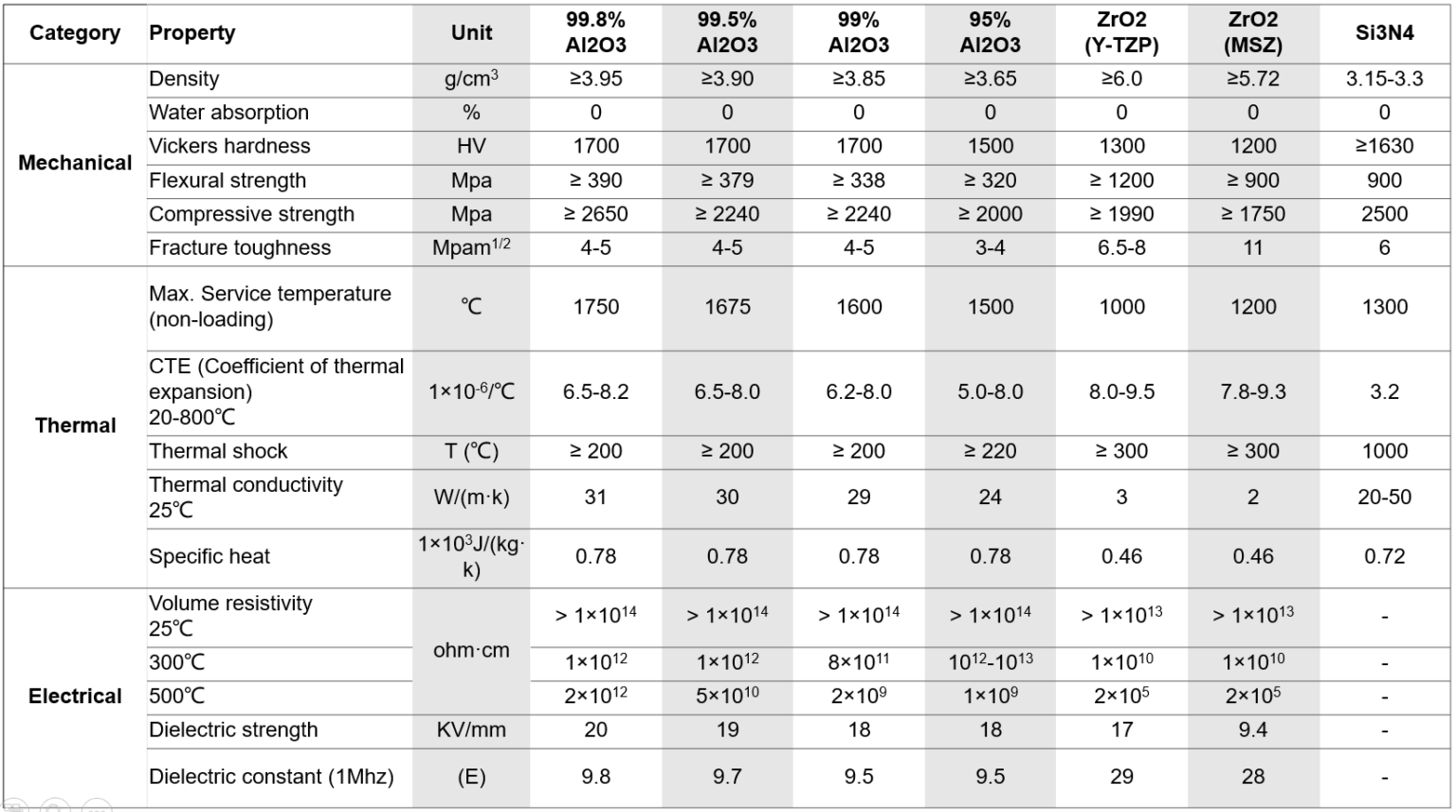
4. Quality inspection method of engineering ceramics
The product testing methods in the table below are the company’s internal control standards and are for customer reference only.
Test Item | Detection Method | ||
---|---|---|---|
Size | Length and Width | Vernier Calipers | |
Thickness | Thickness gauge, micrometer | ||
Shape and Position Tolerances | Straightness, flatness, roundness, parallelism, coaxiality, etc. | Thinner and smaller products: two-dimensional measuring instrument | |
Products with complex shapes: three-dimensional measuring instrument | |||
Surface Roughness | Surface Roughness Tester | ||
Appearance | Clay | Visual inspection, thickness gauge | |
Smudge | Visual inspection | ||
Pit | Visual inspection, graduated microscope | ||
Ceramic Blister | Visual inspection, graduated microscope, thickness gauge | ||
Scratch | Visual inspection, graduated microscope | ||
Convex Ridge | Visual inspection, graduated microscope, thickness gauge | ||
Defect | Visual inspection, graduated microscope | ||
Crack | Visual inspection, visual inspection after soaking in magenta | ||
Performance | Thermal Conductivity | Thermal Conductivity Meter | |
Dielectric Strength | Voltage Breakdown Tester | ||
Volume Resistivity | Comprehensive Analyzer | ||
Density | Density Meter | ||
Vickers Hardness | Hardness Tester | ||
Bending Strength | Universal Tester |
the Future Trends
With the development of modern technology, engineering ceramics have gradually become an important key material for the development of many high-tech fields. Its development in the future will mainly benefit from breakthroughs in material technology, and its development will also largely affect the development and progress of other industries.
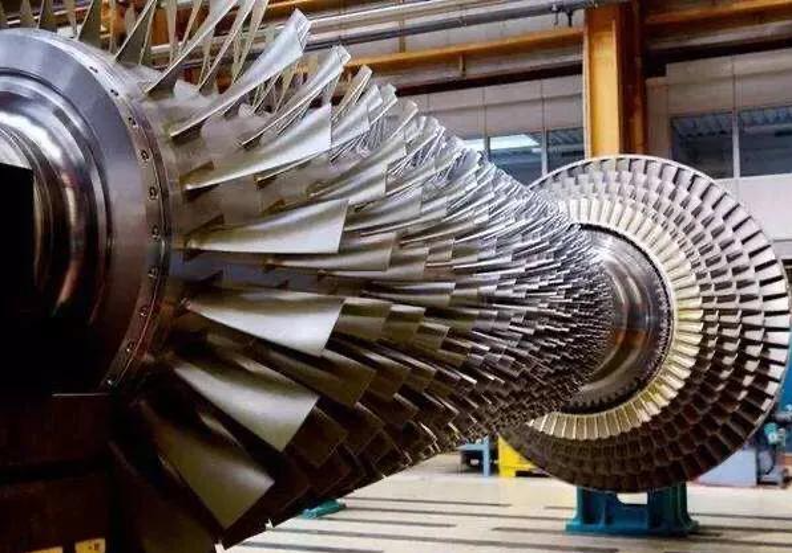
Composite Materialization
Combining engineering ceramics with other materials can obtain composite materials such as ceramic matrix composite materials, cermets, ceramic composite electronic packaging materials and ceramic composite medical materials. They have great potential for development and are widely used in the aerospace field at present, and will develop rapidly in the civil field in the future.
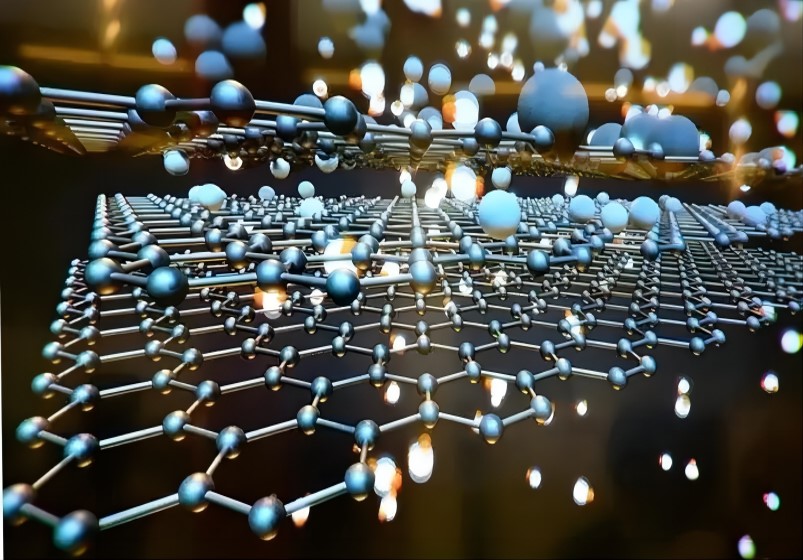
Nanoization
-Ceramic nanotechnology has excellent properties in chemistry, mechanics, light absorption, magnetism, etc., so it will play an extremely important role in future special materials and special technologies, and its application range will become wider and wider.
– At present, the research on nano-ceramic materials is still in its infancy, and many technological problems need to be solved.
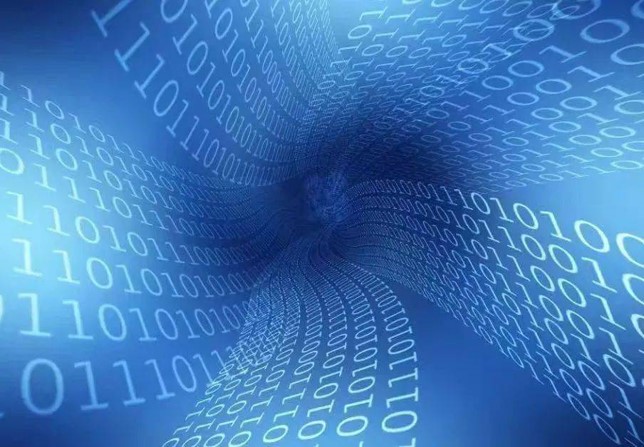
Digitizing
– Design and simulate products through computer-aided design software to improve design efficiency and accuracy.
– 3D printing technology can realize rapid manufacturing and customized production, and can also reduce production costs.
– Real-time monitoring and control of products through sensors and data acquisition systems to improve product quality and performance.
Why Choose Us
As a manufacturer of engineering ceramic products, we have the following advantages. Hope we can have the opportunity to cooperate with you and seek common development.
Rich Experience 01
We have a professional technical team that can provide customized solutions according to customer needs.
Strict Quality Control System 03
We pay attention to quality management, have a strict quality control system, and have passed ISO9001 certification.
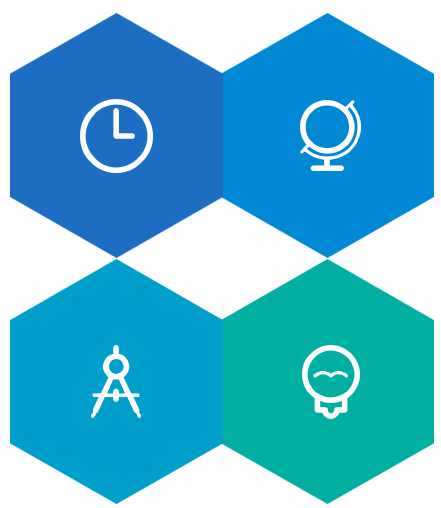
02 Advanced Equipment and Process
The preparation process and quality of the product can be guaranteed.
04 Excellent Service Support
We provide customers with pre-sales consultation, sales follow-up and after-sales maintenance to ensure customer satisfaction.
FAQs
The FAQs (Frequently Asked Questions) column is designed to provide users with fast and convenient answering services. We hope that through the FAQs column, we can help you better understand our products and services. If you have any suggestions or comments on the FAQs column, please feel free to contact us.
1.What should be paid attention to when purchasing engineering ceramic products?
(1) Choose a reliable supplier: The quality of engineering ceramic products is crucial to the use effect.
(2) Understand product performance and quality standards: Before purchasing, it is necessary to understand the performance parameters and quality standards of engineering ceramic products in order to select suitable suppliers.
(3) Clear delivery time and quality standards: When signing a contract, it is necessary to clarify the delivery time and quality standards to avoid subsequent disputes.
(4) Pay attention to logistics and packaging: Engineering ceramic products are usually relatively fragile, so it is necessary to pay attention to logistics and packaging to avoid damage during transportation.
(5) With perfect after-sales service: After-sales service is a strong support to guarantee your rights as a consumer
2.What are the most important performance characteristics of engineering ceramics?
1) Engineering ceramics have high strength and high toughness, which enable them to meet the needs of different industrial applications.
(2) High temperature stability determines its performance in high temperature environment.
(3) Engineering ceramic products are an important wear material, and high wear resistance has an important impact on their service life.
(4) High chemical stability enables engineering ceramic products to be used in some harsh chemical environments, such as acid-base solutions, high-temperature and high-pressure gases, etc., and thus successfully applied in chemical, petroleum, pharmaceutical and other fields.
3.How to solve the problem that the product quality does not meet expectations?
Our company has been focusing on quality and service. If the product quality does not meet the contract requirements, our company will immediately arrange to re-produce qualified products; if we cannot provide qualified products, we will arrange refunds.
4.How to deal with the damage in transportation?
All of our products are packed in safe packages suitable for long-distance transportation, which are not easy to be damaged; in case of damage, please cooperate with our company and logistics company to go to claim process at the first moment, and then our company will arrange replenishment.
5. What Is your core product?
After 15 years of development, our company has formed four advantageous product chains, which are metallized ceramic products, ceramic grinding burrs, ceramic substrates and engineering ceramics. In addition, we can also supply ceramic plates, ceramic tubes, thermostat ceramics, ceramic seals, textile ceramics, spark plug insulators, honeycomb ceramics, etc. All of our products can be customized, and we provide proofing and mass production services.