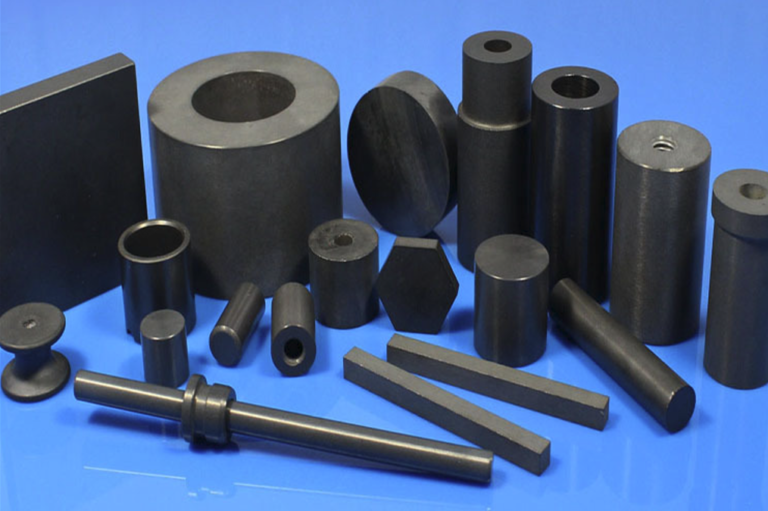
Services for Silicon Nitride Ceramic Parts
Silicon nitride ceramic parts are one of our main engineering ceramics,our capabilities and services are as follows :
- Product type:rods, plates, tubes, discs, bushing, ball, shaft or other shapes;
- Colour: white, grey or off-white
- Material type: RS, HPS,PLS,GPS,SPS;
- Surface finishing: grinding, polishing;
Machining accuracy control
Silicon nitride ceramic products are generally machined to complex geometries using diamond grinding tools. Silicon nitride ceramic parts have visual quality: No cracks, no dark dots, no contamination. Machining accuracy is as follow:
Processing accuracy: can be controlled to 0.002mm;
Cylindricity:best to be 0.005mm;Roughness:best to be Ra 0.2;
Thickness:Min 0.1mm; Smallest aperture: Min. 0.mm;
Concentricity: best to be 0.005mm; Flatness: best to be 0.002mm;
Straight flute: 0.1X100mm; Screw thread: Min. M2
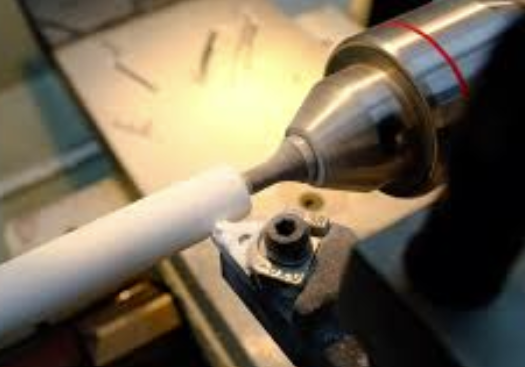
Preparation process of silicon nitride ceramics
Silicon nitride ceramics prepared by different processes, each type of silicon nitride ceramics have different microstructures, which will lead to the performance of the difference is very large.
hot pressed sintering-HPS
gas pressure sintering-GPS
pressureless sintering-PLS
reactive sintering-RS
spark plasma sintering-SPS
Si3N4 ceramic-related composites
Main application of silicon nitride Ceramic Parts
Silicon nitride ceramic materials are characterised by high strength, high modulus, high temperature resistance, oxidation resistance and wear resistance, and are of particular value in working environments with high temperatures, high speeds and strong corrosive media. In addition, Si3N4 ceramics have excellent properties such as high thermal conductivity, thermal shock resistance, low dielectric constant and low dielectric loss, as well as good high-frequency electromagnetic wave transmission properties.
Mechanical
Silicon nitride ceramics are used as bearing balls, rollers, ball seats, moulds, new ceramic tools, pump plungers, shaft cores, etc.
thermal
Use of high-temperature resistance and low heat transfer: the manufacture of heating surfaces for engine components not only improves the quality of the diesel engine and saves fuel, but also improves thermal efficiency.
chemical
silicon nitride ceramics are used as wear and corrosion resistant parts. Such as ball valves, pump bodies, combustion carburettors, filters, etc.
metallurgical
Can make metal material processing moulds, such as tube mandrels, extrusion, wire dies, rolls, conveyor rolls, heat generator fixtures, thermocouple casing, metal heat treatment support parts, crucibles, aluminium conduits, aluminium package lining, etc.