Characteristics of Aluminum Nitride Substrates
Aluminum nitride ceramic substrate is a ceramic substrate made of aluminum nitride (AlN), which has the following characteristics:
1. High thermal conductivity: The thermal conductivity of AlN reaches 180-220 W/(m·K), which is several times or even dozens of times that of traditional ceramic substrates. So aluminum nitride substrates have excellent heat dissipation performance in high-power electronic devices and heat dissipation modules, and can effectively conduct heat away from the device, improving the working stability and life of the device.
2. Excellent electrical insulation: AlN has good insulation properties, high breakdown voltage and low dielectric constant, which can effectively isolate and protect electronic devices.
3. High-temperature stability: Because it can maintain the stability of structure and performance in a high temperature environment, aluminum nitride substrates are widely used in high temperature electronic devices, power modules and other fields.
4. High mechanical strength: Because of its high hardness and strength, good compression and bending resistance, and not easy to crack or deform, aluminum nitride substrates are suitable for applications that need to withstand high loads and impacts.
5. Good dimensional stability: AlN has a low thermal expansion coefficient, which maintains its dimensional stability at high temperature and cooling process, which is beneficial to the assembly of devices and the consistency of performance.
Production Process of Aluminum Nitride Substrates
The forming process of aluminum nitride substrate mainly adopts tape casting method. Tape casting, also known as continuous casting, is a commonly used method for forming ceramic substrates. The method is formed by mixing ceramic powder with a binder to form a slurry, and then uniformly coating the slurry on the workbench of the casting machine. There is a continuously moving mesh belt or roller on the workbench, and the thickness of the coating layer can be controlled by adjusting the speed of the mesh belt or roller.
During the coating process, the slurry will be continuously and evenly extruded from the coating head, and a uniform wet film will be formed on the working table. Then, the wet film goes through a series of processes, such as compaction, drying and sintering, to finally form a ceramic substrate.
The advantage of the tape casting method is that it can realize continuous production with high efficiency. At the same time, the thickness and surface quality of the finished product can be controlled by adjusting the parameters of the casting machine, such as coating speed and pressure. In addition, the tape casting method can also prepare large-sized, thin-walled and complex-shaped ceramic substrates.
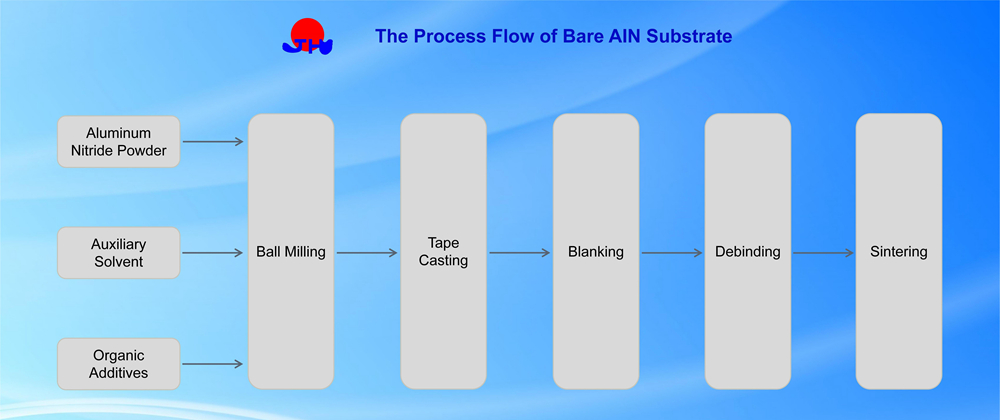
Application of Aluminum Nitride Substrates
Aluminum nitride substrate is a ceramic substrate material with excellent performance, which is widely used in electronics, optoelectronics, aerospace and other fields.
(1) In the field of electronics, aluminum nitride substrates are mainly used for packaging and heat dissipation of high-power electronic devices. Because aluminum nitride has excellent thermal conductivity and insulation properties, it can effectively improve the heat dissipation effect of high-power electronic devices, reduce the temperature of devices, and improve working stability and reliability.
(2) In the field of optoelectronics, aluminum nitride substrates are widely used in the manufacture of LED chips. The aluminum nitride substrate has excellent thermal conductivity and thermal expansion coefficient, which can improve the heat dissipation effect of the LED chip and prolong its service life. In addition, the aluminum nitride substrate also has excellent optical properties, enabling high-brightness and high-efficiency LED light sources.
(3) In the field of aerospace, aluminum nitride substrates are widely used in the manufacture of high-temperature components such as rocket engine nozzles and spacecraft thermal protection materials due to their excellent high-temperature resistance and mechanical properties. Aluminum nitride substrates can withstand high temperatures and severe thermal shocks, protecting spacecraft from damage in high-temperature environments.
(4) Aluminum nitride substrates can also be used in the fields of electronic ceramics, electronic packaging, circuit substrates and microwave devices. Due to its excellent insulating properties, chemical stability, and mechanical strength, aluminum nitride substrates can provide good protection and support, improving device performance and reliability.
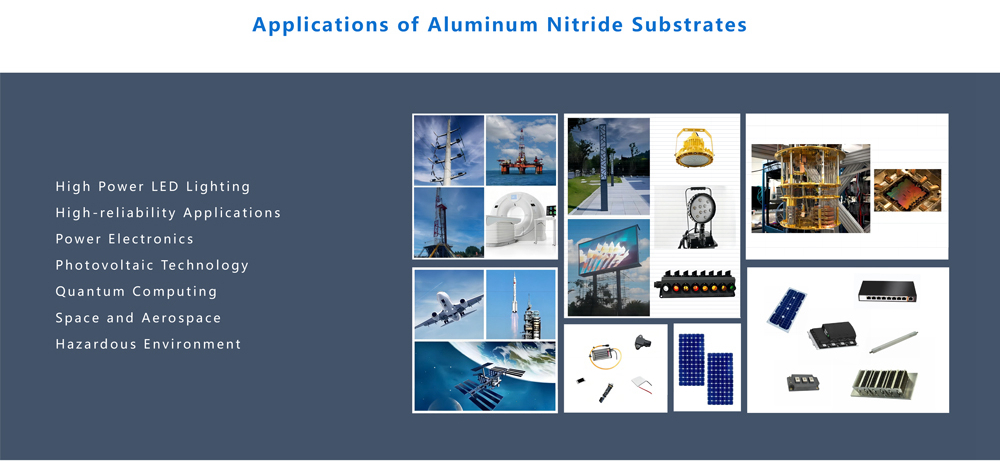
Product Specification
We can produce ceramic substrates of various specifications according to customer drawings. The table below shows our standard thicknesses and sizes.
AlN Ceramic Substrate
|
Thickness(mm) |
Maximum Size(mm) |
Shape |
Molding Technique |
As-fired |
Lapped |
Polished |
Rectangular |
Square |
Round |
0.1-0.2 |
|
50.8 |
50.8 |
|
√ |
√ |
Tape Casting |
≥0.2 |
|
114.3 |
114.3 |
|
√ |
√ |
Tape Casting |
0.38 |
140×190 |
140×190 |
120 |
√ |
√ |
|
Tape Casting |
0.5 |
140×190 |
140×190 |
120 |
√ |
√ |
|
Tape Casting |
0.635 |
140×190 |
200 |
200 |
√ |
√ |
√ |
Tape Casting |
1 |
140×190 |
300 |
200 |
√ |
√ |
√ |
Tape Casting |
1.5 |
|
300 |
200 |
|
√ |
√ |
Tape Casting |
2 |
|
300 |
200 |
|
√ |
√ |
Tape Casting |
2.5 |
|
300 |
|
|
√ |
√ |
Tape Casting |
3 |
|
300 |
|
|
√ |
√ |
Tape Casting |
… |
|
450 |
|
|
√ |
√ |
Isostatic Pressing |
10 |
|
450 |
|
|
√ |
√ |
Isostatic Pressing |
Other special thicknesses within the thickness range of 0.1-3.0mm can be achieved by lapping. |
Why Choose Us
1. Custom sizes & thicknesses are available upon request.
2. Various processings are available (surface lapping & polishing, laser scribing & cutting, metallization, etc.).
3. Sufficient manufacturing capacity and advanced inspection equipments.
4. With sufficient stock for all standard sizes, and with flexible delivery.
5. Stable quality, consistent product specifications for each batch.
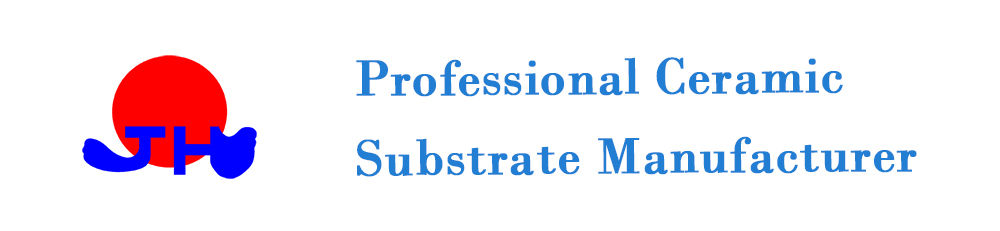