Direct bonded copper substrate is a type of ceramic copper-clad substrate. DBC is a ceramic metallization method that bonds copper foil to the surface of a ceramic substrate.
The preparation process of DBC ceramic substrate is as follows:
First, the treated copper foil is covered on the surface of the ceramic substrate, an inert gas with a certain oxygen content is introduced, and then the temperature is raised. During this process, the copper surface will be oxidized. When the temperature reaches the range where the eutectic liquid phase exists, ceramic and copper will produce a eutectic liquid phase with each other. This liquid phase wets the ceramic and copper at the same time, completing the preliminary connection. Subsequently, during the cooling process, Cu and Cu2O precipitate from the eutectic liquid phase and exist at the connection interface to achieve a tight connection.
The DBC process takes advantage of the copper-oxygen eutectic, which has a lower melting point than pure copper or ceramics. At the melting temperature, the eutectic is the only liquid present, which wets and bonds to both surfaces.
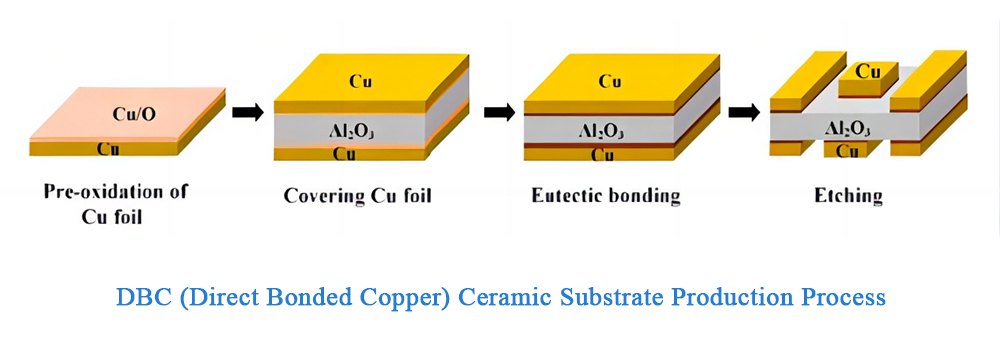
The ceramic materials used in DBC substrates mainly include Al2O3 and AlN, among which alumina is technically more mature than aluminum nitride, and has an advantage in price, so 80% of DBC substrates on the market use alumina.
Product Application
Due to its excellent thermal conductivity and electrical insulation properties, DBC ceramic substrates are widely used in the packaging and heat dissipation of high-power electronic components. Here are some major applications:
1. Packaging of power semiconductor devices: Such as power MOSFET, IGBT, etc. Because these devices will generate a lot of heat during operation, the DBC substrate can effectively conduct the heat to the radiator or other heat dissipation components to ensure the stable operation of the device.
2. Electronic modules: Such as power modules, drive modules, communication modules, etc. These modules usually need to have high power density and heat dissipation capability. The DBC substrate can provide a good heat conduction path, effectively reduce the temperature of the module, and ensure the reliability and stability of the module.
3. LED packaging: Because LEDs generate a lot of heat when they work, the temperature rises, which affects the luminous efficiency and life of the LED. Using the DBC substrate as the LED packaging material can provide excellent heat dissipation performance, effectively reduce the temperature of the LED, and improve its brightness and lifespan.
4. Electric vehicle power supply: In the electric vehicle power supply system, due to the existence of high-power electronic components, the heat problem is particularly prominent. DBC ceramic substrates can be used as packaging materials for electric vehicle power supplies to ensure efficient operation and long life of the power supply system.

Why Choose Us
We strictly follow the requirements of the quality management system and conduct comprehensive and meticulous testing on each product. These tests are designed to ensure that the product's quality and performance meet design and customer requirements.
In the testing process, we use advanced testing equipment and technology, and rely on experienced technicians for operation and analysis. Any products that do not meet the requirements will be repaired, adjusted or eliminated to ensure that only qualified products leave the factory.
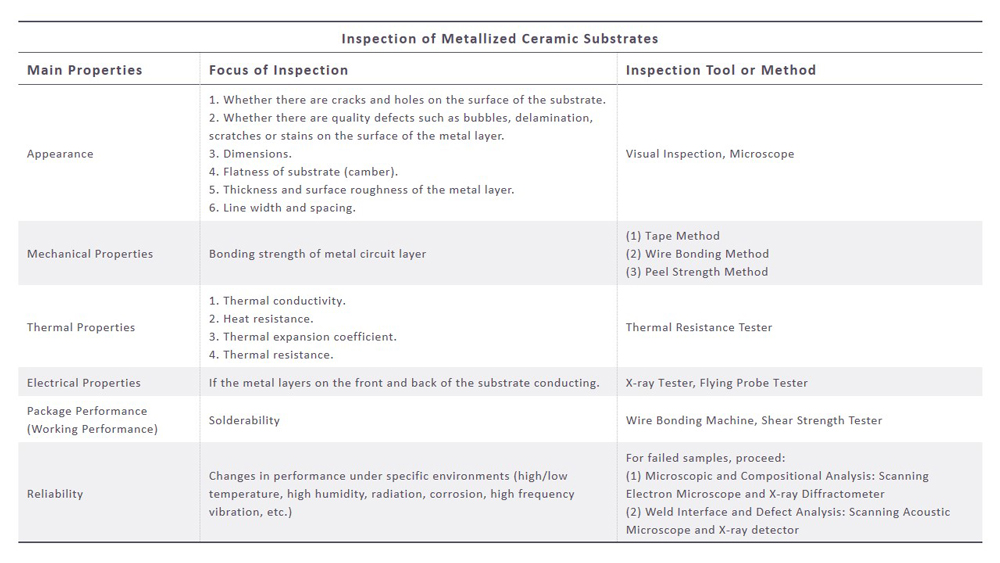