Video
Contents
Metallized Ceramics
We manufacture a variety of refractory Metalized Ceramics, mainly including metallized Ceramic Insulator, Metallized Ceramic Tube, Metallized Ceramic Ring, metallized Ceramic Substrate,Ceramic metallized cylinders.These Metallized Ceramics is fit for high vacuum, high voltage and high pressure applications due to their exceptional insulation strength, superb bonding strength and excellent metal to ceramic joining hermeticity.
Ceramic Grinding Burrs
We can offer a variety of standard types grinding ceramic burr, also customized design ones as client’s requirement including conical burr, flat burr and flat milling disc and so on. When you have any needs of ceramic grinding burr for pepper, salt, spice mill grinder, you can find suitable ones from our products. In addition, we have been supplying many classical types of Pepper Mill Mechanism kit, pepper millstone, Pepper Mill Parts kit. What`s more, we could offer optional grinder mechanism such as stainless steel and carbon steel grinder burrs in it according to different customer needs.
Ceramic Substrates
PCB substrate materials mainly include ceramic substrates, resin substrates, and metal or metal matrix composite materials. Compared with metal and resin substrates, ceramic substrates have outstanding electrical insulation properties, excellent high-frequency characteristics, and better Excellent thermal conductivity, thermal expansion rate, compatibility with various electronic components, stable chemical properties, etc., are more and more widely used in the field of substrates. Ceramic Substrate products are divided into Bare Ceramic Substrate and Metallized Ceramic Substrate according to the production process. They are widely used as substrate materials for different thick films, thin films, and circuits. They can also be used as insulators, as heat conduction paths and in circuits with demanding thermal performance. Used to manufacture various electronic components.
Engineering Ceramics
Engineering ceramic components have physical and mechanical properties, as well as some new ceramics with thermal and chemical functions. They have a precisely controlled chemical composition, which is easy to process according to controlled manufacturing technology and easy to carry out structural design.We are able to provide extensive alumina, zirconia, steatite, cordirite, nitride alumium, silicon carbon and titium oxide ceramic parts.
Dry Pressing
Dry pressing is based on relatively large pressure to press the powder blank in the mold. It is economical and affordable to produce the same variety in large quantities. It is most suitable for parts with not too large geometric dimensions, not too large difference in length and width, and not too complicated shape.
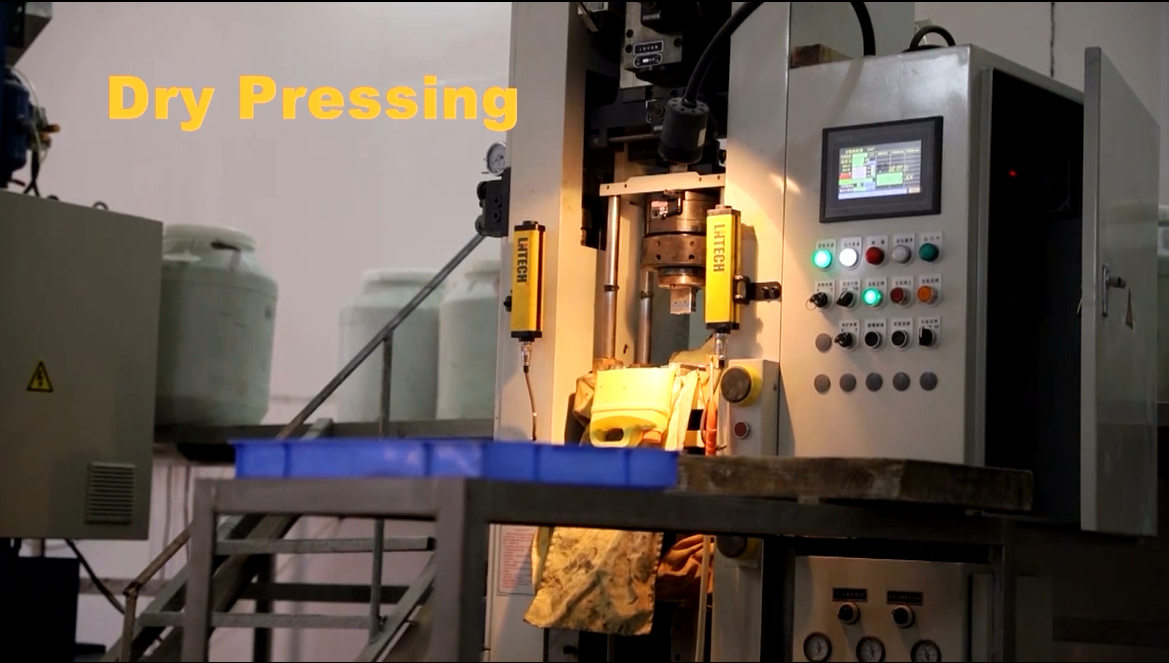
Hot Pressing

Hot pressing is mixed with paraffin wax in the billet. Using the heat flow characteristics of paraffin wax, it is formed under pressure with a metal mold. The condensed body can maintain a certain shape, and the product has precise dimensions, compact structure, and low surface roughness.
Firing
The purpose of sintering is to densify the formed green body, obtain the expected microstructure, endow the material with various properties, make the green body shrink, porosity decrease, density increase, resistivity decrease, strength increase, and grain size increase. Great changes.
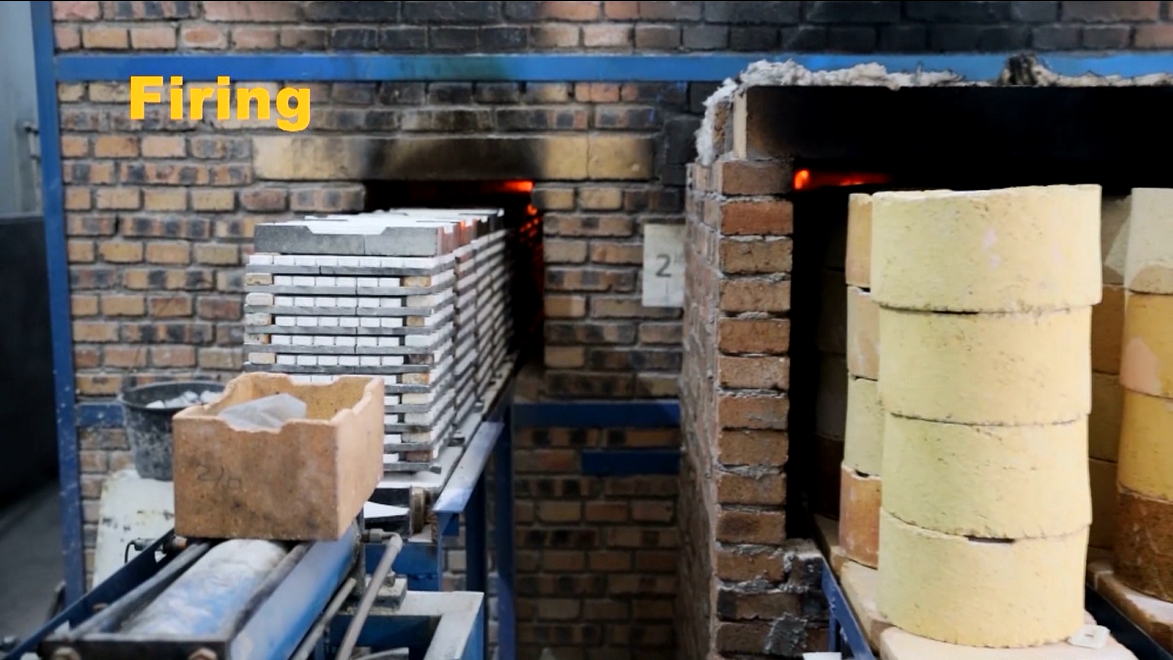
Precision Machining
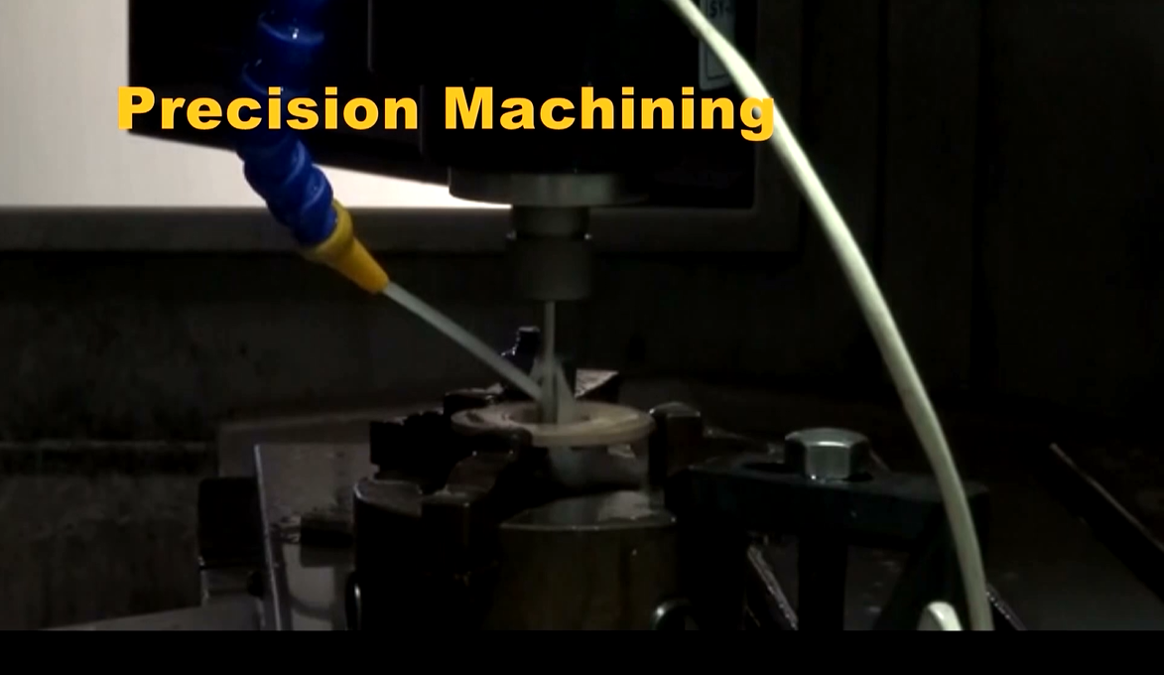
Advanced ceramics must be processed according to user requirements before they can be used as engineering components. This is because although sintered advanced ceramics have a certain shape and size, the dimensional deviation is on the order of millimeters or even larger, which is far from being assembled. The accuracy of the product, and the surface of the product will have adhesion, micro-cracks, etc. to varying degrees, the product must be finished and surface processed.
Precision Grinding
Advanced ceramic grinding is the most common ceramic processing method, which mainly involves research on grinding force, grinding performance, grinding temperature, grinding surface morphology, surface roughness, specific grinding stiffness and grinding ratio, etc. .
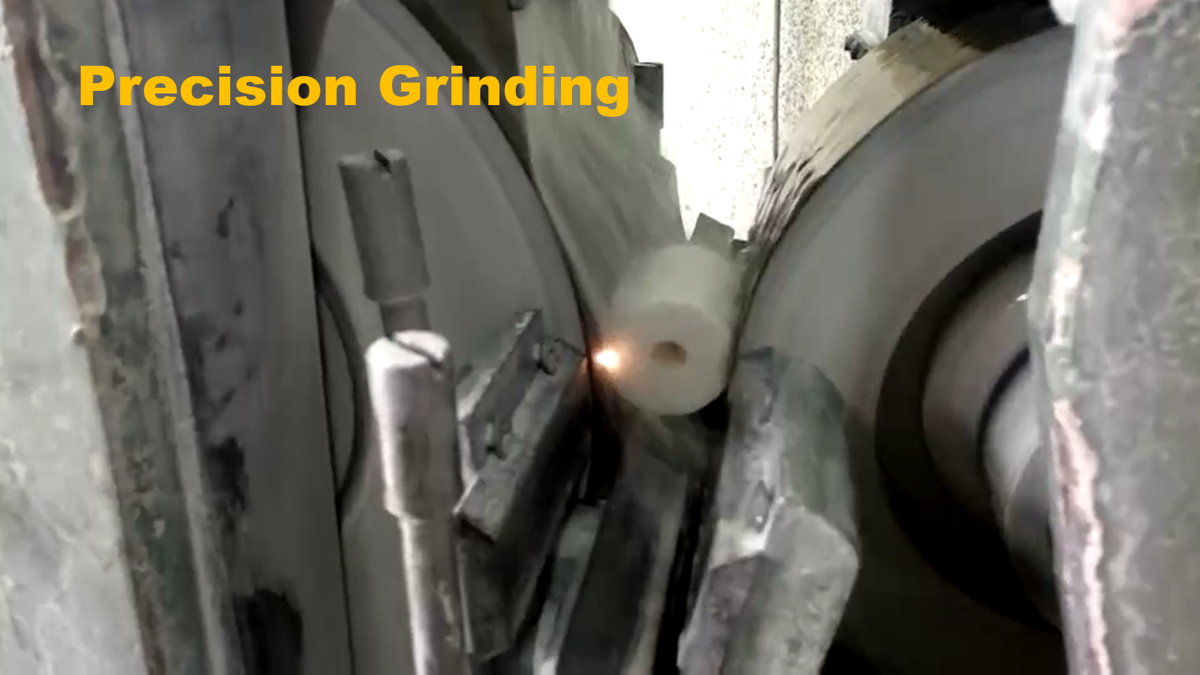
Metallizing process
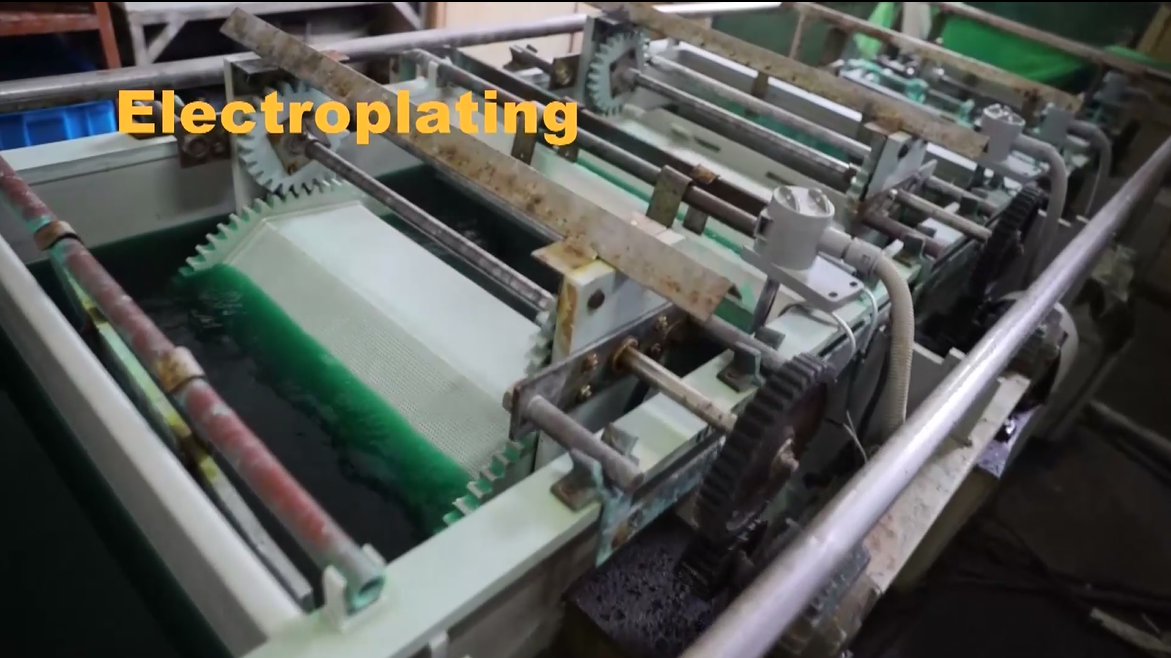
The purpose of ceramic metallization mainly includes the manufacture of electronic components for electromagnetic shielding and metal sealing. There are many metallization methods. In technologies such as capacitors, filters, and printed circuits, silver coating is often used. Others include electroless nickel plating, sintered metal powder, active metal, vacuum vapor deposition, and sputtering.