In this article, we’ll look at the two most common wear resistant ceramics, alumina and zirconia, and see which one is more wear resistant. Furthermore we will analyze their costs and application scenarios. With this information, it will be easier for you to decide whether to use alumina or zirconia for your wear resistant applications.
Table of Contents
Dangers of Wear
Wear refers to the phenomenon that the working surface of an object is constantly lost due to relative motion. Wear means that the geometric size (volume) of the parts becomes smaller.
Wear is a gradual and dynamic process. As wear increases, parts will fail, or completely lose their original functions, or their functions will be reduced and there will be serious damage or hidden dangers. If they continue to be used, they will lose reliability and safety.
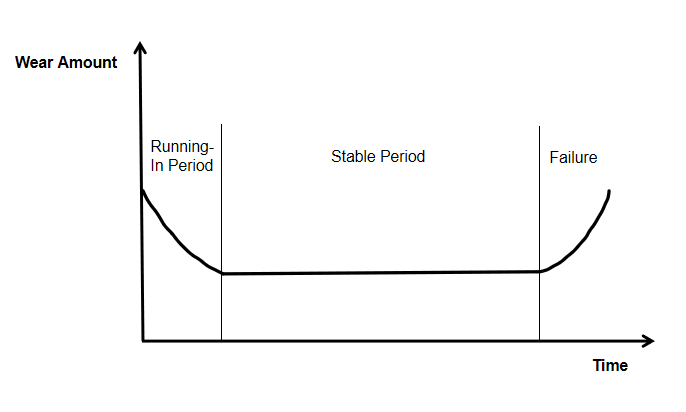
Why Choose Wear Resistant Ceramics
Although wear is an inevitable phenomenon, we can reduce or delay the occurrence of wear. One effective measure is to use wear resistant materials. For example, steel, copper alloys and aluminum alloys among metallic materials, and ceramics and polymer materials among non-metallic materials, can all be used as wear resistant materials.
For high wear environments, wear resistant ceramics are very suitable because of their excellent physical properties and wide range of application scenarios.
Alumina and zirconia are two common engineered ceramics, both of which are often used in high friction and high wear applications. But comparing the two, which one has better wear resistance? Let’s dive in.
Wear Resistance Comparison: Alumina Vs Zirconia
The difference in wear resistance between alumina ceramics and zirconia ceramics can be analyzed from the dimensions of hardness, strength, density, friction coefficient and surface roughness.
Hardness Comparison
The hardness of a material reflects its ability to resist external pressure and scratches. As for advanced ceramics, the higher the hardness, the better the wear resistance.
Both alumina and zirconia ceramics are extremely hard. Natural alumina is called corundum, and has a Mohs hardness of 9 (diamond is 10), which means that alumina is very wear resistant and can resist wear and scratches. Cubic zirconia has a Mohs hardness of 8.5, which is slightly lower than natural alumina, but it is still a very hard material.
Flexural & Compressive Strength Comparison
Flexural strength and compressive strength reflect the ability of a material to resist bending stress and compressive stress. Materials with higher flexural strength and compressive strength are usually more resistant to external pressure and friction, and are less likely to deform and break when worn.
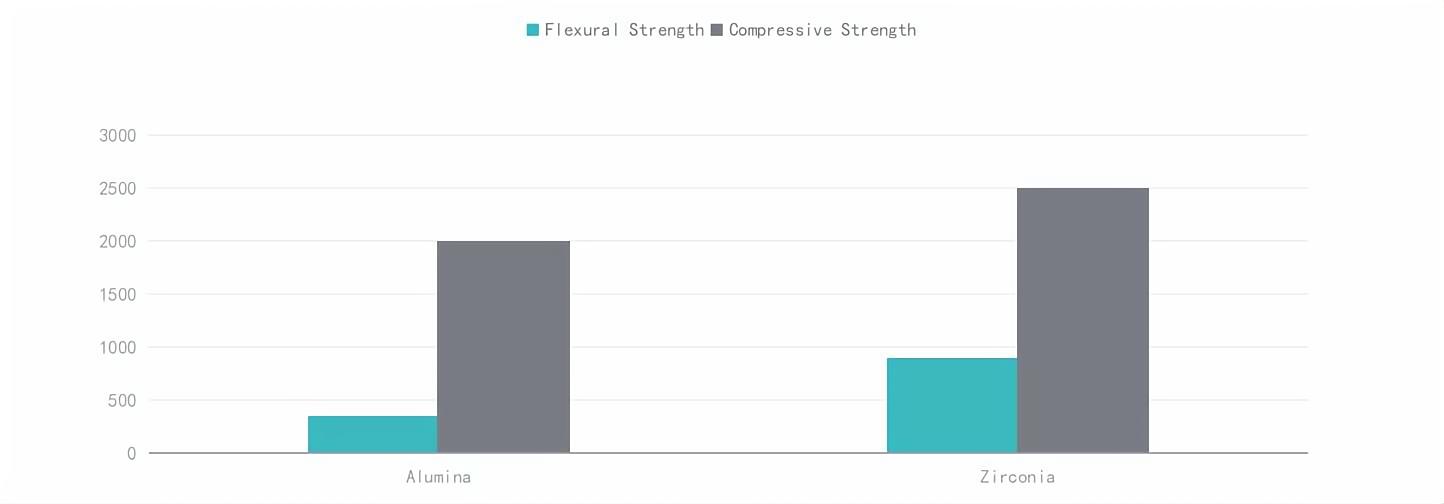
The flexural strength of alumina ceramics is generally 300-400MPa, and the compressive strength is usually above 2000MPa. The flexural strength of zirconia ceramics is very high, generally above 900MPa, and the compressive strength can reach 2500MPa.
Density Comparison
Materials with higher density generally also have better wear resistance. This is because higher density means that the atomic or molecular structure is more compact, making the material stronger and more durable.
The density of alumina ceramics is generally around 3.5g/cm3. The density of zirconia ceramics can reach 6g/cm3, and the texture is finer.
Friction Coefficient Comparison
The lower the friction coefficient, the smoother the surface and the smaller the sliding resistance, which means that the material will wear relatively less during the friction process, thus showing better wear resistance.
The friction coefficient of alumina ceramics is very low, while the friction coefficient of zirconia ceramics is only 1/2 of that of alumina ceramics.
Surface Roughness Comparison
Surface roughness is a characteristic of the microscopic geometry of a surface formed during the machining process of a part. The microscopic protrusions on the rough surface are more likely to produce stress concentration during friction, resulting in increased wear. In contrast, parts with lower surface roughness have a smoother surface, a relatively lower friction coefficient and wear rate, thereby improving the wear resistance of the parts.
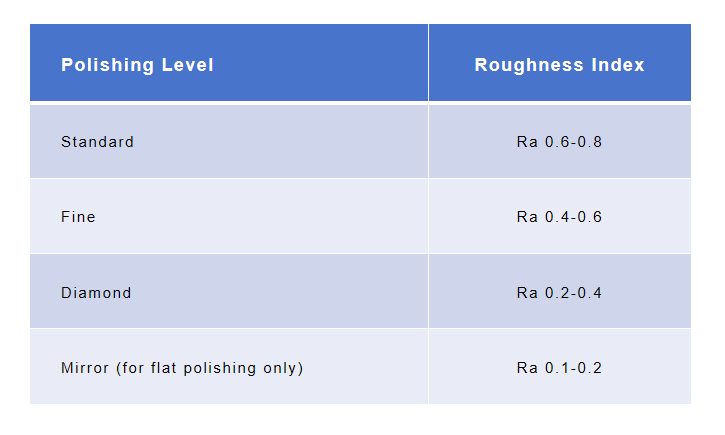
Advanced ceramic products can obtain extremely smooth surfaces through mechanical processing. The surface roughness of 95% alumina ceramics can generally reach Ra0.4-0.6, 99% alumina can reach Ra0.2-0.3, and 99.5% alumina can reach Ra0.2. Zirconia ceramics have higher density and finer texture. After grinding, its surface roughness can reach Ra0.1, which is mirror-like, extremely smooth, and has a lower friction coefficient.
Cost Comparison: Alumina Vs Zirconia
The price of zirconia ceramics on the market is generally higher than that of alumina ceramics.
One reason is the cost of raw materials. Compared with Zr, Al is much more abundant in the earth’s crust and much cheaper. On the other hand, yttria is widely used as a stabilizer for zirconia, in which Y is a rare earth element with limited sources.
The second reason is production cost. Grinding zirconia of the same thickness takes almost 10 times longer than grinding alumina and consumes more diamond tools. In addition, since zirconia requires a higher sintering temperature, the cost of the sintering process is also higher than that of alumina.
Application Scenarios
When choosing wear resistant ceramics, in addition to wear-resistant properties, we also need to consider other factors. For example, for sliding wear, the material needs to be not only tough and mechanically strong, but also resistant to fatigue and thermal stress. It may need to be non-magnetic or electrically insulating. In this case, our choice is alumina ceramic. But for impact wear, we prefer zirconia ceramic.
As for the application of grinding media, in general grinding scenarios, alumina ceramic is competent enough. It has high wear resistance and can ensure the stability and efficiency of the grinding process. But if it is a grinding media that works under centrifugal force, we would choose zirconia ceramic because it has high toughness and impact resistance, and will not break during high-speed collisions.
Conclusion
Zirconia ceramics have better wear resistance than alumina ceramics. However, there are several factors to consider when choosing which ceramic material to use. In addition to performance, we also need to consider their costs and actual application requirements in order to determine the most suitable wear resistant ceramics.